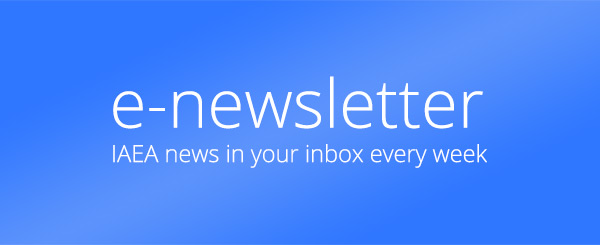
If you would like to learn more about the IAEA’s work, sign up for our weekly updates containing our most important news, multimedia and more.
Decommissioning by Design: How Advanced Reactors are Designed with Disposal in Mind
Joanne Liou
Planning for the end of life from the outset might not be either particularly appealing or a priority. However, when it comes to a nuclear facility’s life cycle, the value in accounting for that end of life is driving designers, vendors and regulatory bodies to address decommissioning upfront. This proactive approach, known as decommissioning by design, draws on best practices and lessons learned from past experience, and implements a ‘by design’ concept that is also applied to nuclear safety, security and safeguards. When decommissioning is considered from the outset, facility developers can make design choices that will make decommissioning safer, more efficient and more cost-effective.
“By taking into account decommissioning in the design stage of a nuclear facility, it is possible to optimize its final phase — its decommissioning — which is mandatory in the life cycle of a reactor,” said Helena Mrazova, a Decommissioning Technology Specialist at the IAEA. Early generations of nuclear power plants (NPPs) were designed with a focus on short-term operational performance, with decommissioning as an afterthought. For example, the designs of some graphite gas cooled reactors built in France in the 1970s did not address how they would be dismantled, and this is now proving difficult to implement.
“We have facilities that are more than 60 metres in height, 30 metres in diameter and with thick walls of more than 5 metres of concrete, housing tonnes of graphite in the reactor core. The dismantling of these reactors is very challenging, because they were simply not designed to be decommissioned. The French electricity utility company EDF (Électricité de France) has recently established a Graphite Reactor Decommissioning Demonstrator (which has also become an IAEA Collaborating Centre) to test, improve and optimize innovative tools and remote handling technologies on full-scale mock-ups and digital 3D models in order to verify the feasibility of decommissioning scenarios and optimize the decommissioning of these reactors,” Mrazova said.
“ By taking into account decommissioning in the design stage of a nuclear facility, it is possible to optimize its final phase — its decommissioning — which is mandatory in the life cycle of a reactor.
Great expectations and opportunities
The aims of decommissioning by design are to better plan the sequence of decommissioning activities, to reduce potential radiation exposure of workers, and to reduce the amount of radioactive waste, thereby lessening the burden on waste facilities and future generations. “Decommissioning by design does not only involve physical design features, it also includes how businesses are structured to plan and conduct the decommissioning activities,” said Marcel Devos, Director of Regulatory Affairs for Prodigy Clean Energy, a developer of marine- and land-based transportable NPPs. Devos formerly managed the Vendor Design Review (VDR) programme at the Canadian Nuclear Safety Commission (CNSC). “Determining funding mechanisms and establishing responsibilities for decommissioning are essential to enable a successful end-of-life process,” he said.
Although decommissioning by design has not been universally adopted, Canada is one country that has taken steps towards this forward-looking practice. The CNSC’s review for reactor vendors includes decommissioning by design, which applies lessons learned from experiences documented by the IAEA and the Nuclear Energy Agency of the Organisation for Economic Co-operation and Development. “Future owners and operators in Canada are increasingly expecting vendors to complete the VDR process and to have a clear plan to resolve gaps that have been identified. Industry is recognizing that end-of-life considerations are a priority in the licensing and environmental assessment processes,” Devos said.
There is growing interest in small modular reactors (SMRs), which are a type of advanced nuclear reactor with a limited power capacity — typically up to 300 MW(e) per reactor. “Developers of the next generation of NPPs, including SMRs, have a tremendous opportunity to address, through the design and deployment process, the social questions associated with the end of life of a nuclear facility, while speeding up decommissioning and reducing waste burdens on future generations,” Devos said.
Decommissioning for SMRs
There are more than 80 SMR designs and concepts in various stages of development around the world. With the portfolio of SMRs varying in size, materials and technology, decommissioning approaches for these advanced reactors will vary. “The decommissioning process will depend on the facility’s design, its accessibility and compactness, as well as a country’s spent fuel and radioactive waste management plans and practices,” Mrazova said.
The modularity of SMRs and their various deployment models could redefine conventional decommissioning practices. Some smaller SMRs, commonly referred to as microreactors, are designed to be factory-assembled and transported as a unit to a location for installation. At the end of life, the module would be returned to the factory of origin to be refuelled or moved to a decommissioning facility. “This approach could reduce costs and the scope of activities taking place in the locality of the power plant, increase nuclear and radiation safety, and increase acceptance of SMR deployment,” Mrazova said. “There is also potential for the standardization of some decommissioning activities, such as the decontamination or dismantling of primary equipment.” However, this approach leaves tasks outstanding, such as the development of specialized dismantling tools and remote handling equipment.
Knowledge of the materials used, such as the type of steel, and of the required standards for steel producers, including the need for very low levels of impurities in order to minimize activation, will positively impact the management of waste from decommissioning. By practising decommissioning by design, impurity levels and the associated cost impacts on dismantling at the end of life could be limited when material composition is addressed carefully beforehand.
“The general rule for decommissioning nuclear facilities, including SMRs, is to have a ‘decommissioning-friendly’ design, underscoring the value of the early approach,” Mrazova said. “The distinguishing features of SMRs, such as their modular design and material selection, should make the decommissioning process more efficient, less costly and reduce the daily dose rate of global workers involved in decommissioning.”
The IAEA is developing a publication focused on the design aspects of SMRs for decommissioning, which is expected to be published in 2024.