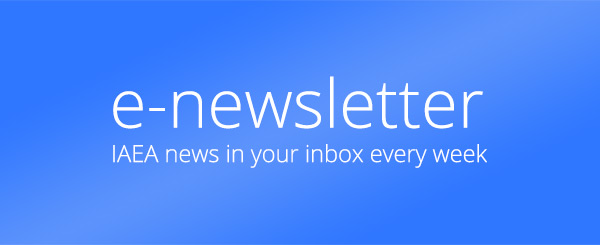
If you would like to learn more about the IAEA’s work, sign up for our weekly updates containing our most important news, multimedia and more.
Closing fusion’s materials and technology gaps
Matteo Barbarino
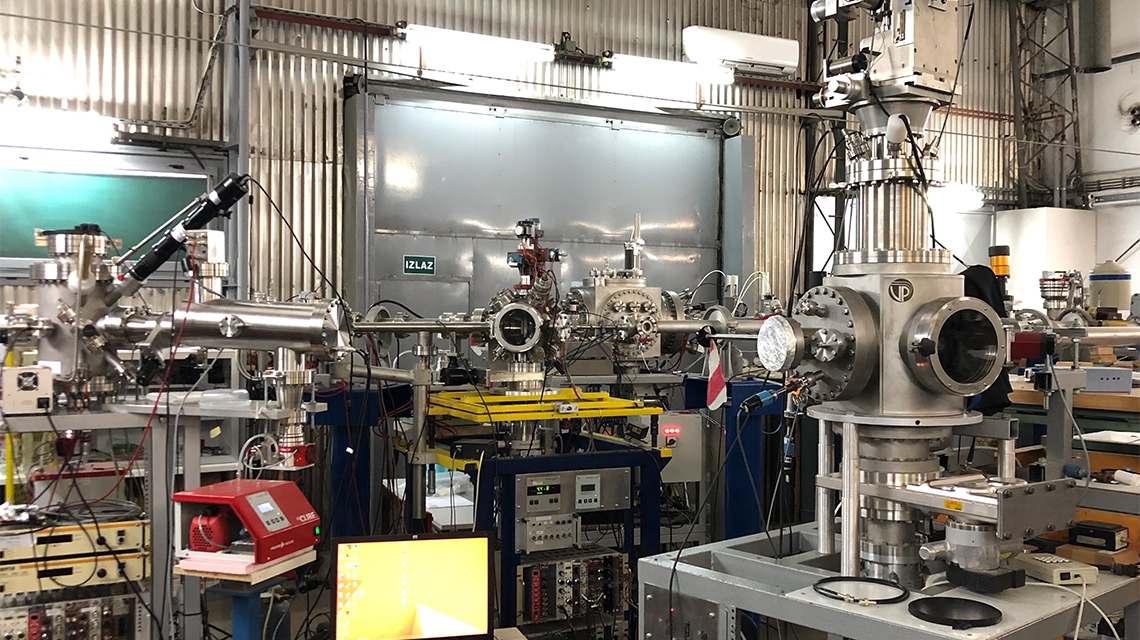
The ‘He Ion Source and DiFU Dual-Beam Facility’ was installed with IAEA support in Croatia’s Ruđer Bošković Institute. (Photo: IAEA)
Closing fusion’s materials and technology gaps
The most challenging science and engineering endeavour on earth is arguably fusion. Building a fusion reactor, achieving a self-sustaining reaction and converting that power to near inexhaustible electricity will change humanity and our relationship with energy forever. As enticing as this may sound, progress has not been easy or smooth. Technical challenges around the structures, fuels and materials needed to hold such complex machines together remain only partially solved.
Understanding the technical limits and gaps of knowledge faced by fusion energy today begins by looking inside the reactor itself.
Inside a tokamak reactor, a super-hot ionized gas or ‘plasma’ is heated to over 100 million degrees Celsius (°C) to induce fusion reactions. Confined by powerful magnetic fields, the walls of the reactor are protected from the volatile plasma.
Plasma used in nuclear fusion is usually made up of two heavy isotopes of hydrogen — deuterium and tritium — which then fuse to produce helium and neutrons. In fusion power plants, engineers hope to ‘breed’ or create additional tritium from the reaction itself with yet untested lithium blanket shielding that reacts neutrons resulting from fusion.
“The energy of the fusion-generated neutrons poses serious challenges to the fusion power plant’s first wall and vacuum vessel, which means considerations need to be given to radiation damage, biological shielding, remote handling, and safety,” explained Ian Chapman, CEO of the United Kingdom Atomic Energy Authority.
Chief among engineers’ tasks is developing high-performance materials that are able to sustain high temperatures and the intense neutron fluxes from the reaction. Understanding the impact of operating conditions on the plasma-facing components is also essential for the future of large-scale fusion power plants.
Materials built for extremes
Creating structural and plasma-facing materials that can withstand degradation from neutrons is a priority for researchers. These materials need safety characteristics such as low neutron-induced radioactivity to minimize the production of radioactive waste. Today, however, there is a lack of specialized fusion irradiation facilities where radiation degradation mechanisms can be tested and materials can be developed and qualified under the necessary conditions.
The IAEA is helping to address issues associated with fusion materials development and research by coordinating the drafting of guidelines for reference material testing techniques, and by bridging knowledge gaps in designing facilities for testing fusion reactor materials and components.
“Technologies like the dual-beam ion facility installed in 2019 at the Ruđer Bošković Institute in Croatia with IAEA support can simulate the conditions that a material would be exposed to in a fusion reactor. These conditions include product transmutation and simulating damage produced by energetic fusion-generated neutrons and particles,” said Melissa Denecke, Director of the IAEA’s Division of Physical and Chemical Sciences.
The main part of a reactor where plasma comes into direct contact with the reactor vessel is known as the ‘divertor’, and scientists and engineers are looking to find its optimal configuration so that it better handles the heat fluxes it encounters. Using knowledge and data acquired from various irradiation experiments and simulation tools, they are also developing and verifying a framework of reactor design criteria for all in-vessel components, divertors included.
A very hot exhaust
Located at the very bottom of a reactor in most designs, where impurities such as helium ‘ash’ are diverted, the divertor acts as the ‘exhaust pipe’ of the fusion reactor and is where any excessive heat is channelled to. This configuration helps to produce ‘purer’ plasmas with better energy confinement — a critical parameter for the performance of a fusion device — ensuring the plasma is hot enough for long enough so that sustained fusion reactions can take place.
In ITER, the world’s largest fusion experiment, the divertor will be made up of 54 ‘cassettes’, each weighing 10 tonnes. The conditions placed on the cassettes will be very demanding; facing steady heat fluxes of 10 to 20 megawatts per square metre, with parts exposed to temperatures of between 1000°C and 2000°C, the cassettes will need to be replaced by remote handling at least once during the machine’s lifetime. To deal with the extreme heat and damaging particles, the components facing the plasma will be armoured with tungsten, a material that has both low tritium absorption and the highest melting temperature of any natural element.
“Although ITER’s divertor design reflects the state of the art of our current understanding and capabilities from a physics and technology point of view, further developments will be required for future fusion power plants. Learning what these are is one of the many important missions of the ITER project,” said Richard Pitts, Leader of the Experiments & Plasma Operation Section at the ITER Organization.
Designing and building future fusion reactors will depend on the technical, technological and material results of ITER and other well-established multinational coordinated research and development activities, but the distance between us and a fusion-powered future continues to narrow every day.